|
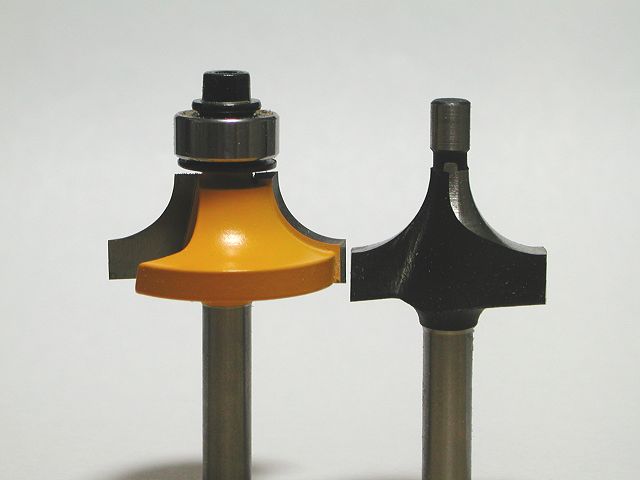 |
|
|
これまでのトリマービット(左 BZ-25G)とハイストリマービット(右 TRB-17H ) 価格差は2.5倍以上ありますので、 なんとなしにハイストリマービットの頼りなさに繋がっているようにも思えます。 ボーズ面ビットはかなり人気が高いのと 切削サイズが近いので以下のテスト用に選びました。
|
|
|
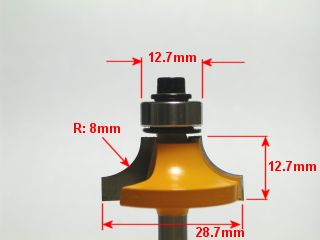 |
|
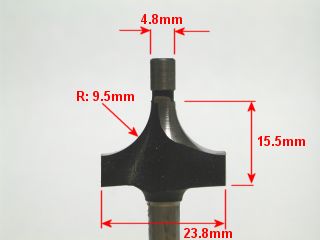 |
|
|
トリマービット使用に必要な各部の寸法の比較。 従来のビットでもインチ規格で決められた部分(12.7mmは1/2インチ)があります。 肝心な切削半径は、8mmに対して9.5mm(3/8インチ)とメートル仕様、インチ仕様の違いがあります。
|
|
|
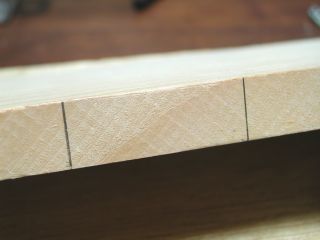 |
|
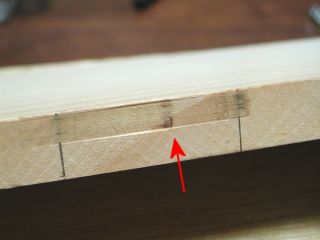 |
|
|
ハイストリマービットの擦れる回転軸がどうなるかの実験。 鉛筆で線を引いた間に当ててみます。
|
|
4-5回、電動トリマーを操作し回転する軸で擦ってみました。 1箇所電動トリマーの移動を止めた所もあり(矢印)そこは焦げています。 こりゃ駄目か??と思ったのですが、
|
|
|
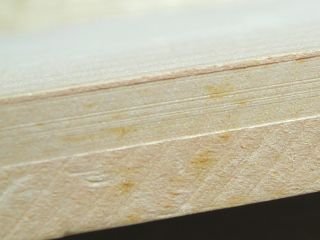 |
|
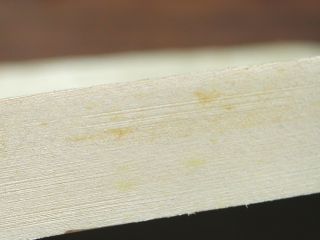 |
|
|
そこで実際の切削速度で2回擦ってみました。 ご覧の通り浅い凹み傷が付いていますが、焦げ目は付かないようです。
|
|
その上をお馴染の替刃式ヤスリ(M-20GP)で研磨しました。 これなら全く問題ありません。 (木材に付着したシミのお陰で同じ場所だと言う事が判ります。)
|
|
|
以上で回転軸で擦る事によるガイドでも全く支障ないことが判ると思います。 コロ付きのビットと違うところは木口面を成
形後に研磨する事で、作業手順を考えてやるだけで済み難しい事はありません。
それでも精神衛生上良くない! と思われる方は、次に掲げる別なガイドを併用する方法でやればこすれの問題は全
くなく加工することが出来ます。
|
|
|
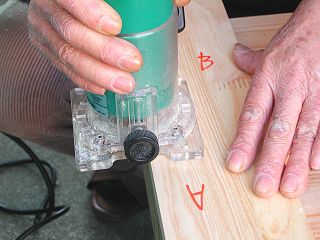 |
|
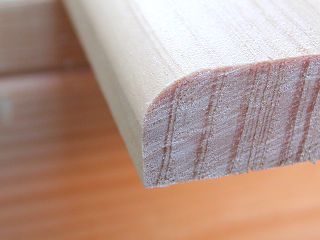 |
|
|
公称板厚15mm(実測15.3mm)の集成材の縁を丸く削り落とす実験。 最初にBZ-25Gを使って加工します。
|
|
片面を削り終わりました。 極普通のボース面です。
|
|
|
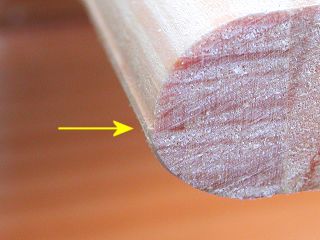 |
|
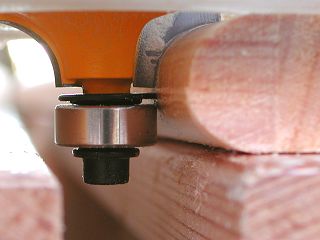 |
|
|
続けて反対側の角を削ったのですが、何と後から削った部分は余計に削りこまれ、段差が出来てしまいました。
|
|
その原因はこれです。 コロが当たるガイドとなる面が既に削られてしまったので、更に内側に当たり深く削りこんでしまったのです。
|
|
|
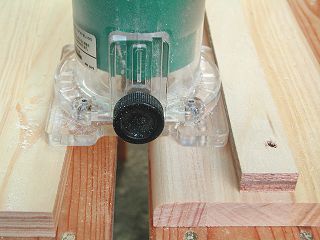 |
|
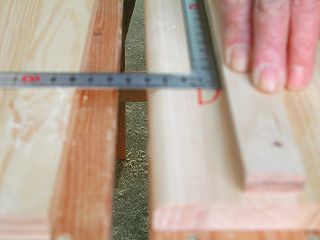 |
|
|
その解決策。 片方を削り終ったらガイド板(右の幅狭の板)をトリマー台座に当てます。
|
|
そしてトリマーを外し加工する板の端からガイド板までの距離を測ります。 (この写真だけ地面にピントが合ってしまいました。 失礼!)
|
|
|
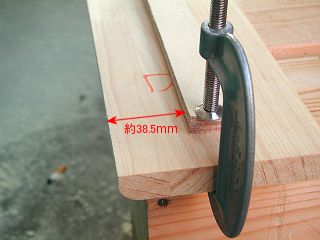 |
|
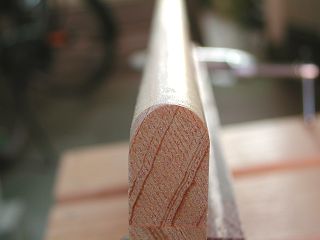 |
|
|
そして反対側の面の測った距離と同じ位置にガイド板を固定します。
|
|
そして切削すれば削りすぎの段差がなく加工できます。 実はこの時にコロは全く仕事をしていません。 同じ原理をハイストリマービットでも使えばよいのです。
|
|
|
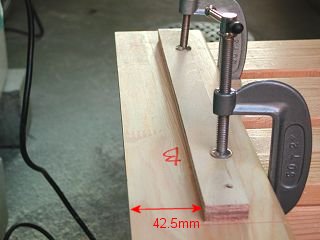 |
|
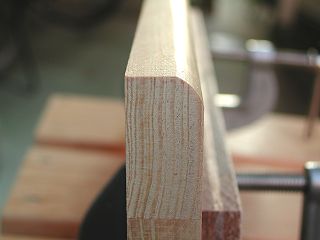 |
|
|
ハイストリマービット先端の太さを5mmとしてその半分をトリマー台座の中心からの距離(45mm)より差し引き、42.5mm離れた位置にガイドを固定します。
|
|
そして片面を削り終わりました。 回転する軸先端は木口に接触していませんので、擦り傷は全く無しです。
|
|
|
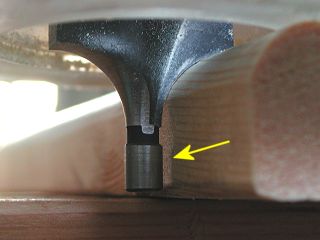 |
|
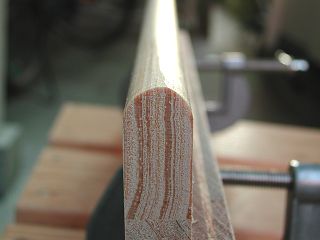 |
|
|
切削後電動トリマーを当ててみたクローズアップ。 ご覧のように回転軸先端(矢印の先)は木口に触れていません。
|
|
反対側の角も同じ手法で切削して完成。
|
|
|
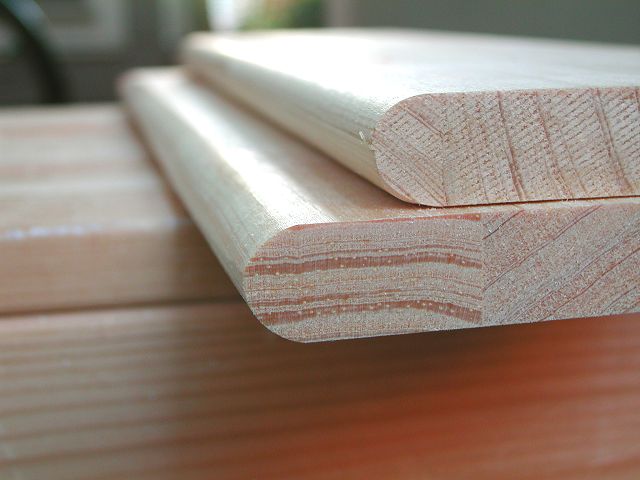 |
|
|
BZ-25Gで成形したもの(上)とTRB-17Hで成形したもの(下)の比較。 切削半径は前者が8mm、後者は9.5mmと違 いますが、こうして見るとその差は殆ど目立たない領域と言えます。 よって私はあまり気にしないのですが、それよりも
ビットの大きな価格差の方が問題です!
|
|
如何だろうか? ハイストリマービットは無い無いずくしの日曜大工を標榜する私にぴったり来る工具だ。 勿論種類が10種類しかない事や堅い木では無理なので、相変わらず黄色いビットのお世話にもならなければならないシチュエーションも起きるが、トリマー使用未体験の方やコストを抑えながらいろいろ楽しみたい方には超お奨め品である。 Copyright (C) 2001-2019, Vic Ohashi All rights reserved.